Aluminium manufacturers must stay trained in the latest technology and be aware of new trends to stay competitive. This is because aluminium remains one of the world’s most popular fabrication and construction materials.
Since the day that bauxite was first refined and inventors and engineers heard about the properties of this amazing new metal, the world’s industries have clamoured for the material. When the metal’s properties were first being explored in the early 1800s, it was considered more valuable than gold. As the smelting process of aluminium became more refined and streamlined and aluminium became more commonly available, the value of the metal fell while its popularity in manufacturing soared.
Modern Aluminium Manufacturing Processes
Today’s aluminium manufacturers have to be experts in the processes involved in designing and manufacturing the aluminium products and those that treat and finish the products. They have to maintain a plant that can meet the manufacturing requirements of their customers and still keep an eye on up-and-coming technologies and trends that would improve those customers’ products.
The manufacturers serve customers in industries including:
- Electronics
- Automotive parts
- Solar Cells
- Robotic components
- Laboratory equipment
- Furniture
- Construction materials
In manufacturing the many complex and exacting parts and components of these industries, the manufacturers must also be well-versed in the CAD design process used to create the 3D models and specifications for the aluminium products.
They have to have a complete knowledge of how to adapt these digital plans and models to the three-dimensional capabilities of a CNC machine. These complicated machines have revolutionised the manufacturing process and turned into a much more dynamic and precise practice. The machines interpret the CAD drawings and turn them into raw aluminium products.
The product may be designed to be produced by the extrusion process. This is where molten aluminium is forced through a small aperture to form lengths of tubing, channels, pipes and conduit. The extrusion process lines up the molecules of the aluminium and interlinks them to form a stronger finished product.
But a finished product may still need to be sealed and treated to better prepare it for its intended use. Anodising and powder coating are two of the most popular sealing treatments in today’s manufacturing processes.
Anodising is an electrochemical process that transforms the surface into a durable surface that offers a higher level of corrosion resistance than itself and is also available in a range of colours. Powder coating is a dry powder that’s applied to the aluminium’s surface with an electrostatic charge to bind it to the surface. The coating is then cured with a heat lamp or ultraviolet light.
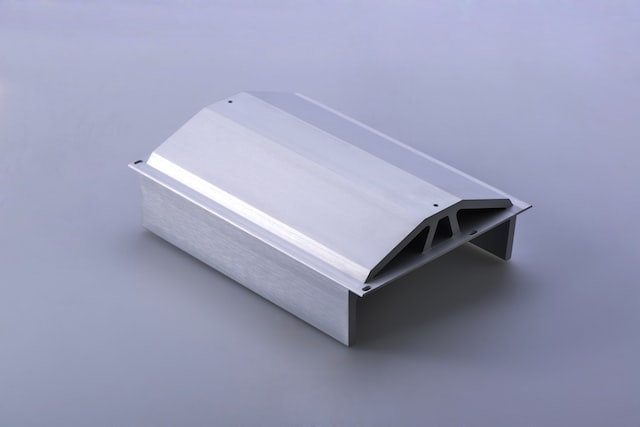
Partner with Experience
Your company’s reputation relies on the quality of the components of the manufacturer you use. You want to partner with a manufacturer experienced in providing all the steps required in the manufacturing process. Gold Star Metal is an aluminium manufacturer in Thailand with almost thirty years of experience in all the aspects of modern aluminium production. Find out what Gold Star Metal can offer you.